
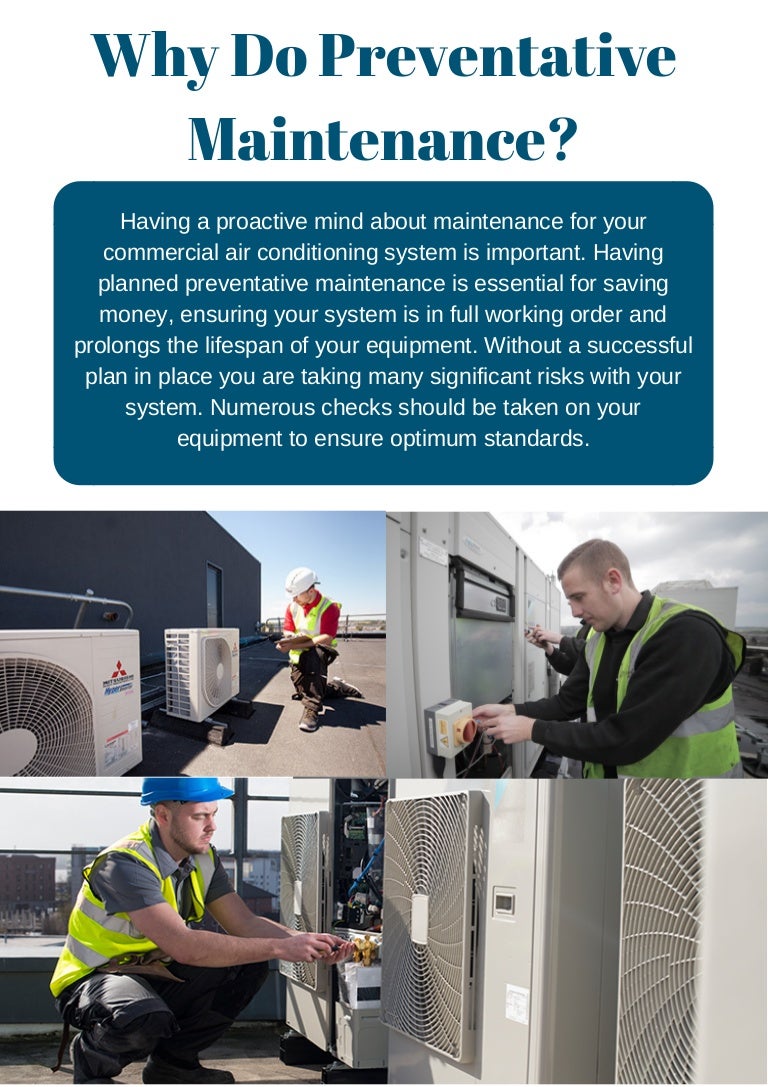
time elapsed since the last change (100 hours).the ideal time between oil changes (200 hours).Say the equipment is used for an average of 10 hours daily. It is difficult to line up resources for the change if you don't know when the equipment is going to complete 200 operational hours. With time-based maintenance, you know that your equipment is due for an oil change, say after every 200 operational hours. Usage-based maintenance considers both, the time elapsed since the last maintenance and the average number of operational hours to schedule PM tasks. This system creates necessary work orders as the due date approaches, after which the maintenance action is triggered.Ĭonsider adding major utilities, equipment, tools, and technology your business depends on for its success to create a time-based maintenance plan for your business. Time-based maintenance occurs at scheduled calendar intervals to comply with manufacturer recommendations. To safeguard and future-proof critical equipment, businesses use these four major types of preventive maintenance methods: Preventive maintenance is typically performed on critical equipment that have high impact and associated downtime costs.Planned unscheduled maintenance is usually applied to inexpensive and easy to replace equipment that do not have a major impact on operations in case of failure.Under planned maintenance, you can schedule preventive or unscheduled maintenance depending on the needs of the asset, and its impact on operations. The goal of planned maintenance is to reduce downtime and costs, as well as to increase asset and equipment lifespans. The concept of planned maintenance lies at the heart of preventive maintenance strategies.
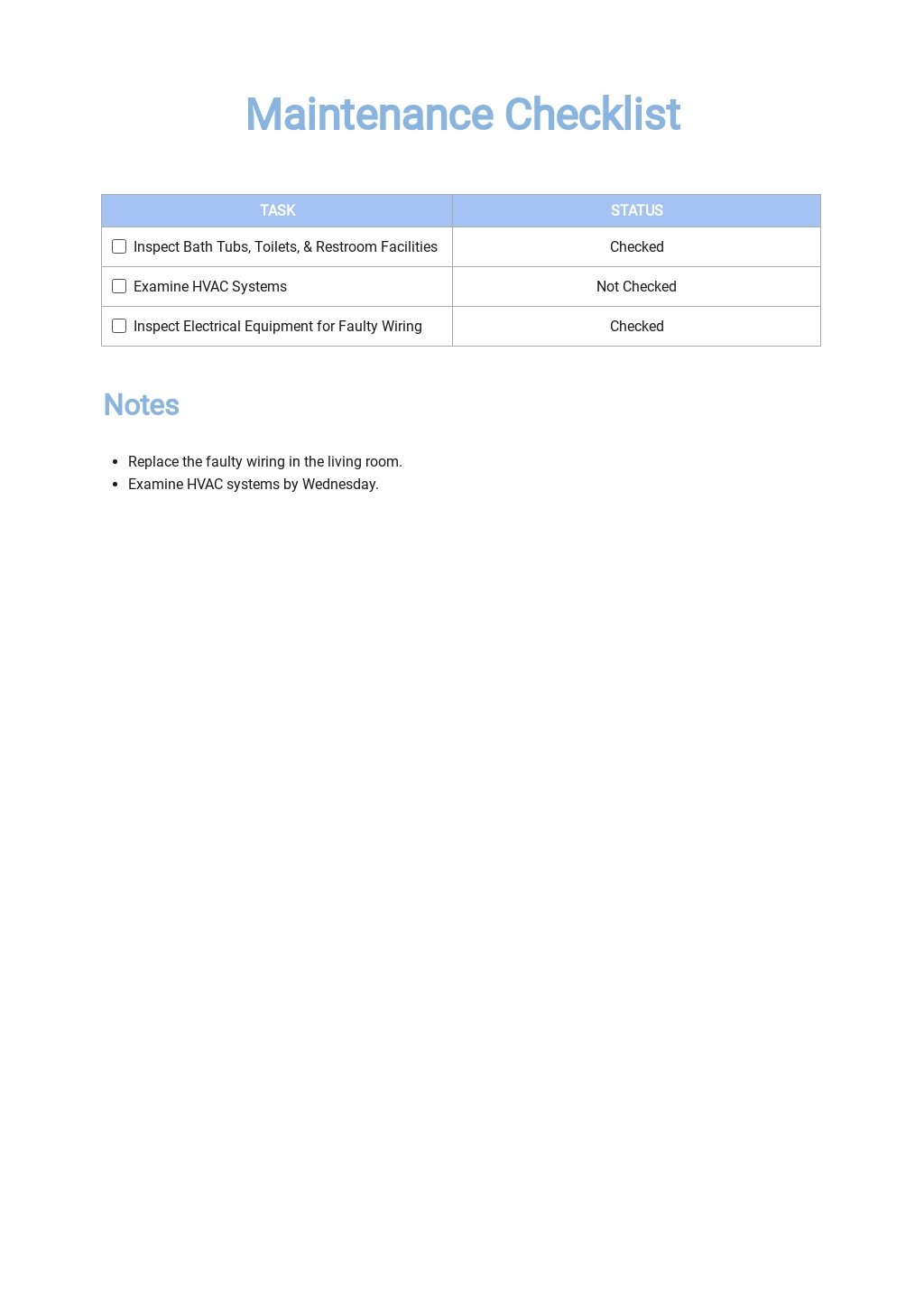
What are the different types of preventive maintenance? Using this data, you can determine which assets will benefit from PM.įor maximum RoI from your PM program, consider assets which have a significant impact on operations, are prone to failures, or are expensive to replace. It helps reduce instances of unexpected equipment failures and costly unplanned downtimes, and instances of expensive reactive, and breakdown maintenance.īusinesses use computerized maintenance management systems (CMMS) to plan PM strategies and schedule PM tasks.ĬMMS records information about asset lifecycle history, maintenance records and reports, performance, and faults and failure incidents for every equipment being monitored. Preventive maintenance (or preventative maintenance) is the regular, planned and routine maintenance performed to maximize the longevity of assets, equipment, and buildings. This is precisely what preventive maintenance (PM) helps achieve. This approach may work perfectly for SMEs with few properties and assets to track.Ī recent report by Senseye found that large facilities lose an average of 27 hours a month to machine failures, and $532,000 for each hour of unplanned downtime.Įnterprises need a "fix it so it stays healthy" strategy to avoid unexpected failures that result in costly unplanned downtime. In this "don't fix it if ain't broke" approach to Operations & Maintenance, technicians attend to assets/equipment only in the event of fault/failure. It is an easy start since it doesn't require complex maintenance plans or implementation. Reactive maintenance (also known as run-to-failure maintenance) is the oldest and, to date, a popular maintenance strategy. and save costs on expensive run-to-failure maintenance.
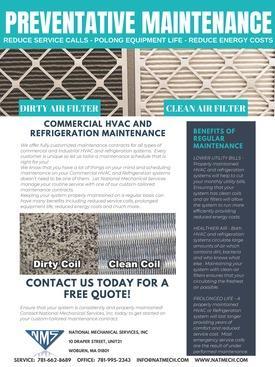
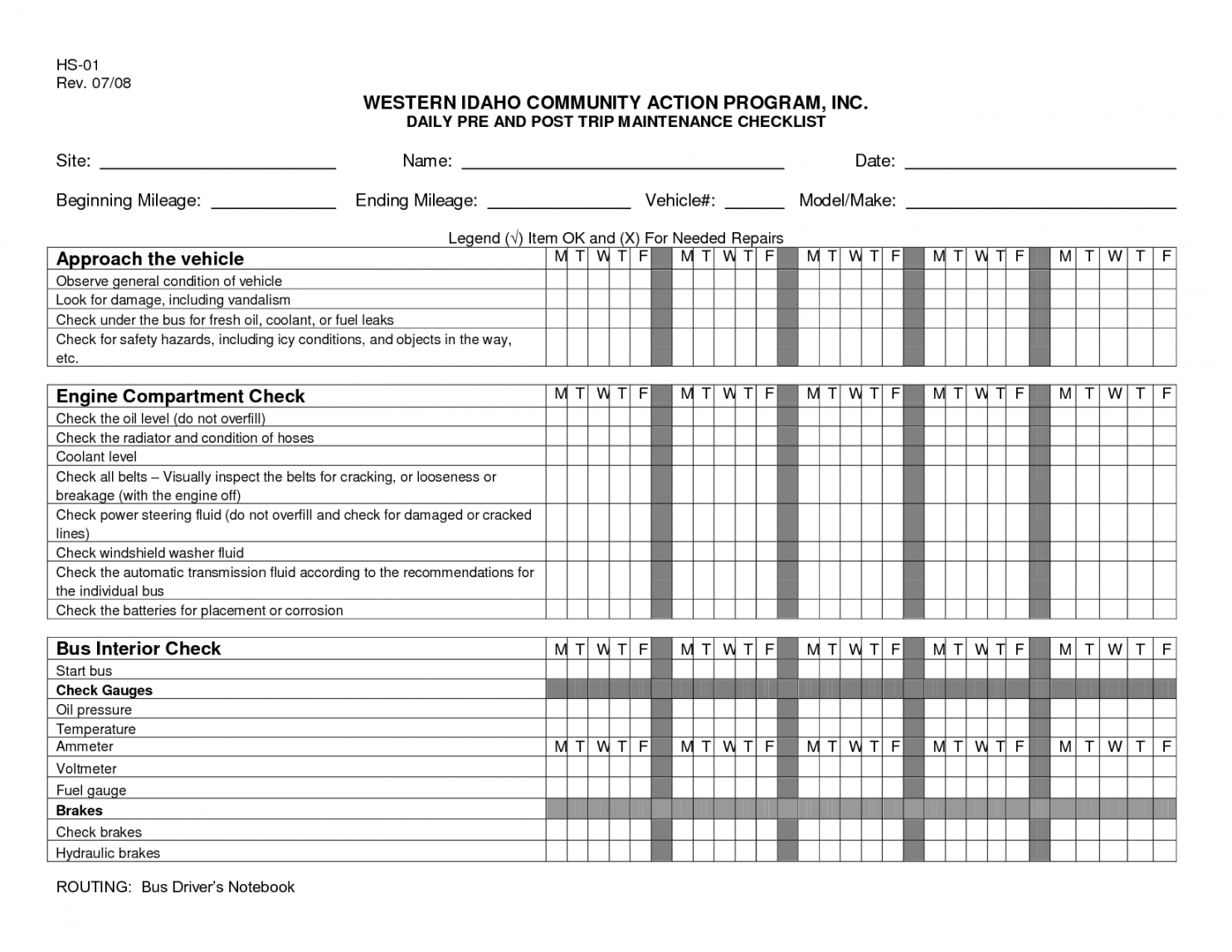
The primary goals of any organization's maintenance management program are standard.
